مبدل های حرارتی پوسته و لوله، تجهیزاتی هستند که به منظور انتقال حرارت بین سیالات در فرآیندها و صنایع مختلف مورد استفاده قرار میگیرند. این تجهیزات، به عنوان متداولترین و پرکاربردترین انواع مبدلهای حرارتی شناخته میشوند. در این مقاله، به معرفی کاربرد، نحوه عملکرد، ساختار، انواع، استانداردها، مزایا و معایب مبدل های حرارتی پوسته و لوله میپردازیم. در انتها نیز، به برخی از متداولترین سوالات مرتبط با این تجهیزات فرآیندی پاسخ میدهیم.
مبدل حرارتی چیست ؟
مبدل گرمایی، مبدل حرارتی یا «مبادله کننده حرارتی» (Heat Exchanger)، وسیلهای است که به منظور انتقال حرارت از یک سیال به سیال دیگر در سیستمهای گرمایش و سرمایش مورد استفاده قرار میگیرد. حرارت بین سیالات در این وسایل، به صورت مستقیم (ترکیب دو سیال) یا غیر مستقیم منتقل میشود. مبدل های حرارتی از تجهیزات پرکاربرد در گرمایش محیط، سرمایش محیط، تبرید، نیروگاه، کارخانه شیمیایی، کارخانه پتروشیمی، پالایشگاه نفت، پالایشگاه گاز و تصفیه فاضلاب هستند.
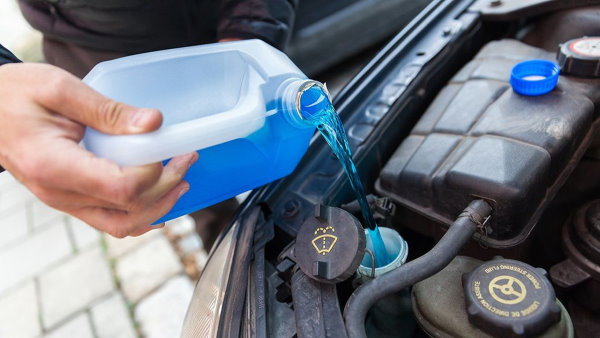
انواع مبدل های حرارتی کدام هستند؟
از متداولترین انواع مبدلهای حرارتی میتوان به مبدل های حرارتی پوسته و لوله، مبدل های حرارتی دو لوله، مبدل های حرارتی صفحه ای، مبدل های حرارتی تودرتو، کندانسورها، اواپراتورها و بویلرها اشاره کرد. از میان انواع مختلف این وسایل، مبدلهای حرارتی پوسته و لوله، رواج و کاربرد بیشتری دارند.
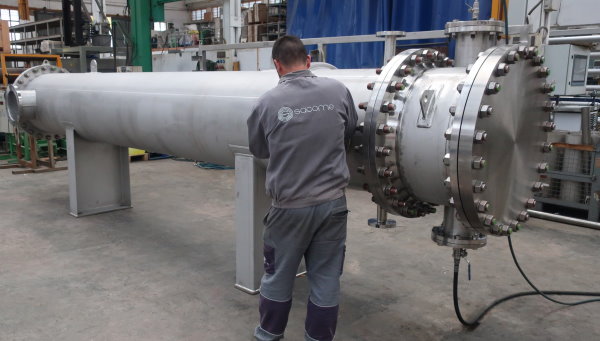
تقسیمبندی مبدلهای حرارتی بر اساس آرایش جریان، ساخت (روش، المانهای مورد استفاده، جنس مواد سازنده) و مکانیزم انتقال حرارت انجام میگیرد. بر اساس این معیارها، انواع مبدل های حرارتی عبارت هستند از:
- انواع مبدل حرارتی بر اساس آرایش جریان سیالات
- مبدل حرارتی همسو
- مبدل حرارتی ناهمسو
- مبدل حرارتی متقاطع
- مبدل حرارتی ترکیبی
- انواع مبدل حرارتی بر اساس روش ساخت
- مبدل حرارتی بازیاب و رکوپراتور
- مبدل حرارتی مستقیم و غیر مستقیم
- مبدل حرارتی استاتیک و دینامیک
- انواع مبدل حرارتی بر اساس المان سازنده
- مبدل حرارتی لوله ای (مبدل حرارتی پوسته و لوله)
- مبدل حرارتی کویلدار
- مبدل حرارتی صفحه ای
- مبدل حرارتی فشرده (فین دار)
- مبدل حرارتی با چرخ آدیاباتیک
- انواع مبدل حرارتی بر اساس جنس ماده سازنده
- مبدل حرارتی مسی
- مبدل حرارتی تیتانیوم
- مبدل حرارتی فولاد ضد زنگ
- مبدل حرارتی گرافیتی، سرامیکی، کامپوزیتی، پلاستیکی و غیره
- انواع مبدل حرارتی بر اساس مکانیزم انتقال حرارت
- مبدل حرارتی تک فازی
- مبدل حرارتی دو فازی
مبدل حرارتی پوسته و لوله چیست ؟
«مبدل حرارتی پوسته و لوله» (Shell and Tube Heat Exchanger)، یکی از متداولترین انواع مبدل های حرارتی است که معمولا در پالایشگاههای نفت و کارخانههای فرآیندی بزرگ مورد استفاده قرار میگیرد. این نوع مبدل، از یک مخزن تحت فشار (پوسته) و مجموعهای از لولههای موازی نزدیک به هم (باندل) تشکیل میشود. مبدل های حرارتی پوسته و لوله بر اساس اصول انتقال حرارت به روش هدایت گرمایی کار میکنند. با جریان یافتن سیالات درون لولهها، انتقال حرارت از سیال گرم به سیال سرد و برعکس انجام میگیرد. به این ترتیب، سیال درون سیستم به دمای مورد نظر میرسد و برای استفاده مجدد از درون مبدل خارج میشود.
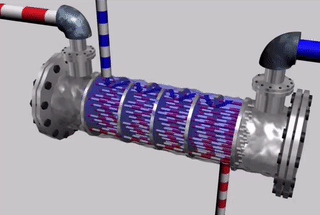
کاربرد مبدل های حرارتی پوسته و لوله چیست؟
مبدل های حرارتی پوسته و لوله در خنکسازی، پیش گرمایش، تولید بخار، بازیابی بخار و عملیاتهای مشابه کاربرد دارند. از متداولترین حوزههای کاربرد این مبدلها میتوان به صنایع به نیروگاهی، تاسیسات سرمایشی، سازههای آبی، کارخانههای کاغذسازی، سیستمهای تبرید، داروسازی، تجهیزات هوای فشرده، رنگکاری صنعتی، معدنکاری و متالورژی اشاره کرد.
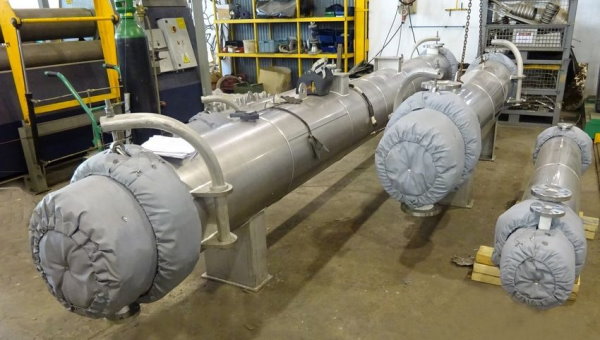
انواع بسیار زیادی از مبدلهای حرارتی پوسته و لوله در بازار موجود هستند. قابلیتها، مزایا و محدودیتهای هر یک از این مبدلها با یکدیگر تفاوت دارند. البته انعطافپذیری بالا در طراحی این نوع مبدل حرارتی، امکان استفاده از آن در صنایع مختلف و شرایط عملیاتی متفاوت را فراهم میکند.
نحوه کار مبدل حرارتی پوسته و لوله چگونه است؟
مکانیزم مبدل های حرارتی پوسته و لوله، بر اساس عبور سیال گرم از درون سیال سرد و انتقال غیر مستقیم حرارت (عدم ترکیب شدن سیالها) است. این نوع مبدل حرارتی، از یک پوسته و مجموعهای از لولهها تشکیل میشود. یکی از سیالها از درون پوسته و سیال دیگر از درون لولهها عبور میکند. طی این فرآیند، انتقال حرارت بین دو سیال صورت میگیرد. به عبارت دیگر، سیال سرد، حرارت سیال گرم را میگیرد.
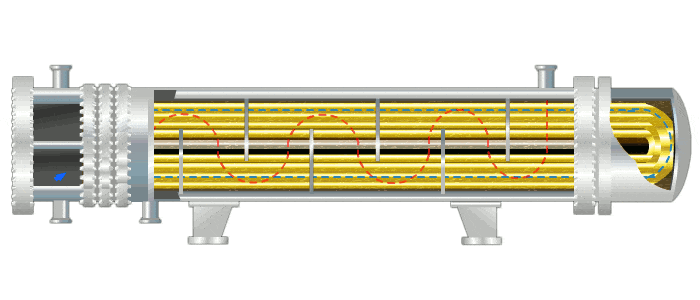
تصویر متحرک بالا، مکانیزم عملکرد یک مبدل حرارتی پوسته و لوله U شکل را نمایش میدهد. در این مبدل، سیال سرد از درون مجرای ورودی زیر پوسته (اصطلاحا مجرای سمت لوله یا سمت کانال)، وارد سیستم شده و با عبور از مسیر لولهها، به صورت گرم (با دمای بالاتر)، از بالای پوسته (مجرای سمت لوله) خارج میشود. سیال دیگر (سیال ورودی از مجرای سمت پوسته)، با عبور از مسیر پوسته و اطراف لولهها، به صورت سرد (با دمای پایینتر)، از سیستم خارج میشود.
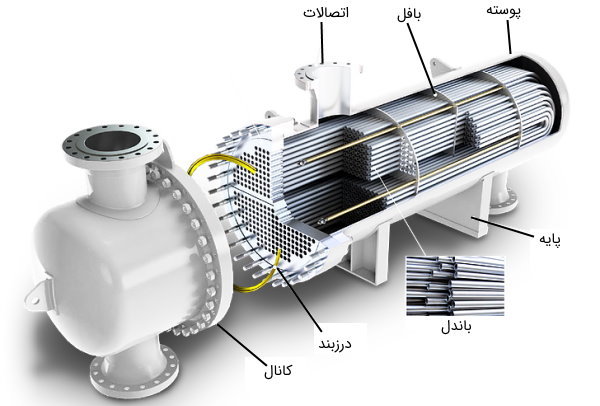
در مبدل حرارتی پوسته و لوله، میزان انتقال حرارت بین دو سیال، به میزان تماس سیال درون پوسته با سطح اطراف لولهها بستگی دارد. این پارامتر، تابعی از تعداد لولههای موجود در مبدل است. در تصویر بالا، هر دو مجرای ورودی و خروجی سمت لوله در یک سمت پوسته قرار دارند. این پیکربندی، به معنای زوج بودن مسیرهای عبور سیال از درون لولهها است. در صورت فرد بودن تعداد مسیرها، مجرای خروجی بر روی بخش عقب پوسته تعبیه میشد. افزایش تعداد مسیرها، ضریب انتقال حرارت را افزایش میدهد. در بخش بعدی، به معرفی اجزای مبدل های حرارتی پوسته و لوله میپردازیم.
اجزای مبدل های حرارتی پوسته و لوله چه هستند؟
پوسته، مجرای سمت لوله، لولهها (باندل)، تیوب شیت، کانال سمت لوله، مجرای سمت پوسته، بافل و میلههای نگهدارنده از اجزای اصلی در مبدل های حرارتی پوسته و لوله هستند.
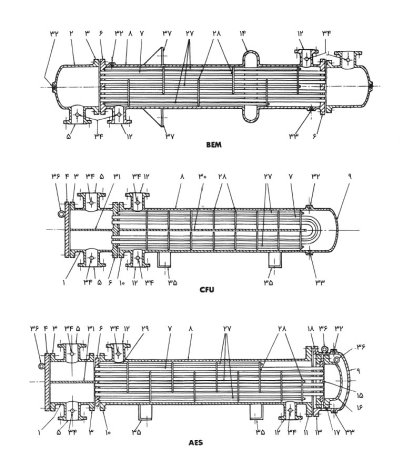
در تصویر بالا، اجزای مختلف مبدل حرارتی پوسته و لوله نوع BEM (ثابت)، CFU (منحنی شکل) و AES (سری شناور) علامتگذاری شدهاند. عنوان هر یک این اجزا عبارت است از:
- کلگی ثابت جلو (کانال)
- کلگی ثابت جلو (درپوش)
- فلنج کلگی ثابت جلو
- پوشش کانال
- نازل کلگی ثابت (مجرای سیال سمت لوله)
- تیوب شیت ثابت
- لولهها
- پوسته
- پوشش پوسته
- فلنج پوسته در کلگی ثابت جلو
- فلنج پوسته در کلگی عقب
- نازل پوسته (مجرای سیال سمت پوسته)
- فلنج پوشش پوسته
- درز انبساطی
- تیوب شیت شناور
- پوشش کلگی یا سری شناور
- فلنج کلگی شناور
- وسیله پشتیبان کلگی شناور
- اتصال حلقه برش
- فلنج اسلیپان
- پوشش کلگی شناور
- دامن تیوب شیت شناور
- فلنج آببندی
- آببندی
- دنبالگر آببندی
- رینگ فانوسی
- میلههای نگهدارنده و اسپیسر
- بافلهای عرضی یا صفحات نگهدارنده
- بافل یا صفحه مانع
- بافل طولی
- جداکننده مسیر
- خروجی هوا
- مجرای تخلیه
- اتصال ابزار دقیق
- زین نگهدارنده
- قلاب حمل و نقل
- پایه گونیایی
برخی از اجزای بالا برای دیگر انواع مبدلهای معرفی شده در استاندارد TEMA هستند. در ادامه، به توضیح برخی از مهمترین اجزای مشترک در تمام مبدل های حرارتی پوسته و لوله میپردازیم.
لوله مبدل حرارتی پوسته و لوله
لوله یا به طور دقیقتر «تیوب» (Tube)، از مهمترین اجزای مبدل های حرارتی پوسته و لوله به شمار میرود که وظیفه تامین سطح مورد نیاز برای انتقال حرارت، بین سیالات را بر عهده دارد. لولههای مبدلهای حرارتی پوسته و لوله، معمولا از جنس مس یا آلیاژهای فولادی با اتصالات بدون درز یا جوشی هستند. لولههایی از جنس نیکل، تیتانیوم یا آلومینیومی، معمولا برای کاربریهای خاص استفاده میشوند. ساخت لولههای بدون درز طی فرآیند اکستروژن و ساخت لولههای جوشی طی فرآیند نورد انجام میگیرد. لولههای جوشی، صرفه اقتصادی بیشتری دارند.
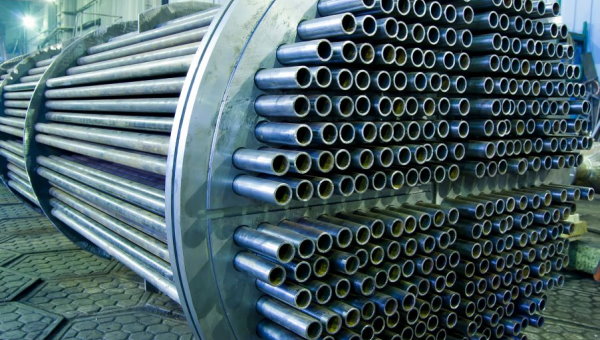
سطح خارجی لوله های مبدل های حرارتی پوسته و لوله، از نوع ساده یا پرهدار است. لوله پره دار، برای سیالاتی با ضریب انتقال حرارتی بسیار پایین مورد استفاده قرار میگیرد. سطوح این لوله، مساحت انتقال حرارت سیالات را نسبت به سطوح لوله ساده، دو تا چهار برابر بیشتر میکنند. قطر لوله های مبدل حرارتی پوسته و لوله معمولا برابر ۱۶ میلیمتر، ۱۹ میلیمتر و ۲۵ میلیمتر است. امکان استفاده از لولههای کوچکتر از این ابعاد نیز وجود دارد. با این وجود، هر چه قطر لوله کمتر باشد، تمیزکاری آن دشوارتر خواهد بود.
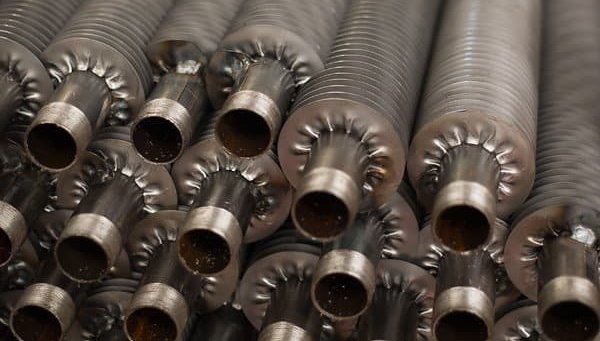
لولههای دارای قطر بزرگتر، به منظور سهولت تمیزکاری یا کاهش افت فشار مورد استفاده قرار میگیرند. ضخامت دیواره لولههای مبدل حرارتی پوسته و لوله بین ۱٫۶۵ میلیمتر تا ۲٫۷۶ میلیمتر تغییر میکند. ضخامتهای پایین، در هنگام استفاده از لولههایی از جنس مواد نسبتا گران (مانند تیتانیوم) انتخاب میشوند. به مجموعه لولههای درون مبدل، «باندل» (Bundle) میگویند.
آرایش لوله مبدل حرارتی پوسته و لوله
آرایش لولههای مبدلهای حرارتی پوسته و لوله، به صورت مثلثی (۳۰ یا ۶۰ درجه) و مربعی (عادی یا دوران یافته) است. آرایش مربعی، در شرایطی مورد استفاده قرار میگیرد که نیاز به تمیزکاری مکانیکی سطح لولهها باشد. در طرف مقابل، آرایش مثلثی، امکان استفاده از تعداد لولههای بیشتر در فضای برابر را فراهم میکند.
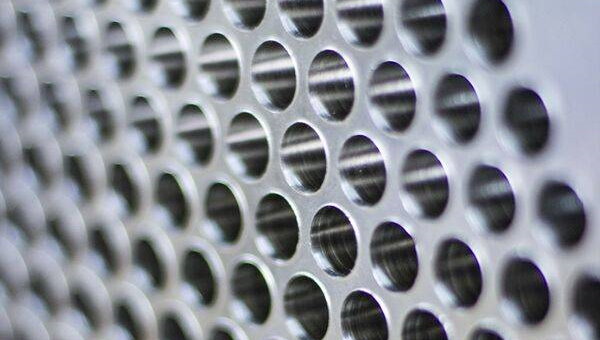
گام لوله در مبدل حرارتی پوسته و لوله
به نزدیکترین فاصله بین مرکز لولهها، «گام» (Pitch) میگویند. این فاصله، معمولا بین ۱٫۲۵ تا ۱٫۳۳ برابر قطر خارجی لولهها است. گام لوله، بر روی افت فشار و سرعت سیال در سمت پوسته تاثیر میگذارد. الگوی گام لوله در اغلب موارد به صورت مثلثی است. این الگو، باعث افزایش میزان انتقال حرارت و تراکم ساختار مبدل میشود. با این وجود، تمیزکاری مکانیکی مبدل های پوسته لوله با الگوی مربعی سادهتر است.
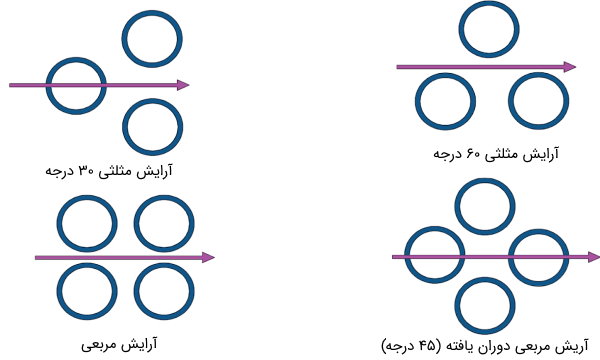
تیوب شیت مبدل حرارتی پوسته و لوله
صفحه لوله یا «تیوب شیت» (Tubesheet)، یک صفحه دایرهای است که به منظور نگهداری لولهها مورد استفاده قرار میگیرند. لولهها، از درون حفرههای موجود در صفحات عبور میکنند. لوله و تیوب شیت، توسط شیارهای سطحی یا جوشکاری به یکدیگر متصل میشوند. دلیل این کار، جلوگیری از ترکیب شدن سیال سمت پوسته با سیال سمت لوله است.
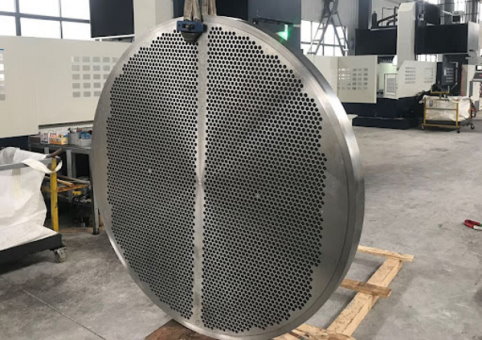
مبدل های حرارتی پوسته و لوله، به غیر از نوع U شکل، از دو تیوب شیت تشکیل میشوند. اتصال لوله و صفحه به گونهای است که از انبساط مکانیکی المانها جلوگیری میکند. استفاده از صفحات دوبل، احتمال ترکیب سیالات را کاهش میدهد. در این حالت، فضای بین دو تیوب شیت در معرض فشار اتمسفر قرار میگیرد. به این ترتیب، نشت هر یک از سیالات، در کوتاهترین زمان ممکن تشخیص داده میشود. تیوب شیت باید از مقاومت مناسب در برابر خوردگی ناشی از تماس با سیالات و سازگاری الکتروشیمیایی خوب با ماده سازنده لوله برخوردار باشد.
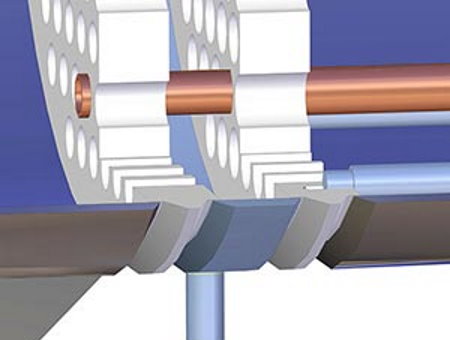
کلگی
کلگی، بخش ابتدایی و انتهایی مبدل و محل قرارگیری مجراهای هدایت (ورود و خروج) سیال درون لولهها است. این بخش از مبدل حرارتی پوسته و لوله، وظیفه کنترل جریان سیال سمت لوله را بر عهده دارد. به دلیل خورندگی بیشتر سیالات سمت لوله، سطح کلگی و مجراهای آن، توسط آلیاژهای مقاوم در برابر خوردگی پوششدهی میشوند. به دو بخش انتهایی مبدل حرارتی پوسته و لوله، کلگی جلو و کلگی عقب میگویند. کلگی میتواند به صورت «کلاهک» (Bonnet) یا کانال باشد.
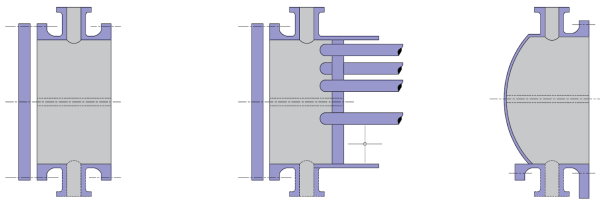
دو انتهای کانال لوله، دارای پوششهای دایرهای با اتصال فلنجی هستند. در صورت نیاز به بازرسی میتوان این پوششها را بدون اختلال در پایپینگ سمت لوله باز کرد. در مبدلهای حرارتی کوچک، معمولا از کلگی و نازلهای فلنجی یا پیچی به جای کانال و پوشش کانال استفاده میشود.
پوسته مبدل حرارتی پوسته و لوله
«پوسته» (Shell)، محفظه دربرگیرنده لولههای مبدل های حرارتی پوسته و لوله است. این محفظه، معمولا توسط نورد یک ورق فلزی و جوشکاری محل درز طولی ساخته میشود. البته امکان ساخت پوستههای کوچک، توسط برش دادن لولههایی با قطر مناسب نیز وجود دارد. میزان گردی پوسته بر روی حداکثر قطر بافل قابل استفاده و احتمال نشت بین پوسته و بافل تاثیر میگذارد.
مجراهای مبدل حرارتی پوسته و لوله
بر روی نوع استاندارد مبدل های حرارتی پوسته و لوله، چهار مجرا (دو مجرای ورودی و دو مجرای خروجی) تعبیه شده است. ورود و خروج سیالات از طریق این مجراها صورت میگیرد. در مبدلهای حرارتی با تعداد مسیرهای فرد، مجراهای هدایت سمت لوله بر روی کلگی جلو و عقب قرار داده میشوند. مجراهای هدایت سیال سمت پوسته، معمولا به صورت متقابل و معکوس بر روی پوسته قرار دارند. تصویر پایین، این پیکربندی را به خوبی نمایش میدهد.
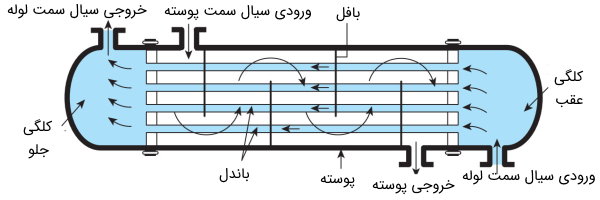
صفحه انحراف جریان
در مسیر نازلهای ورودی، معمولا یک صفحه انحراف جریان تعبیه میشود. این صفحه، از برخورد مستقیم جریان سریع سیال به ردیف بالایی لولهها جلوگیری میکند. برخورد مستقیم سیال به لوله، احتمال فرسایش، کاویتاسیون و یا ارتعاش را افزایش میدهد. از اینرو، به منظور تعبیه مناسب صفحه انحراف جریان و جلوگیری از افت فشار بیش از حد جریان سیال، الگوی لولهها، معمولا به صورت دایره ناقص اجرا میشود.
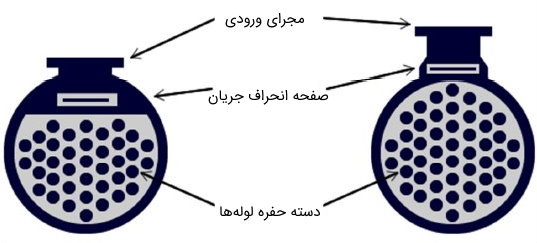
سیال سمت لوله
«سیال سمت لوله» (Tube Side Fluid)، سیالی است که معمولا از طریق مجرای کلگی جلوی پوسته، وارد پوسته میشود. سپس، از درون لولهها عبور میکند. با رسیدن سیال به کلگی عقب پوسته، جریان آن به سمت مسیر دیگر لولهها (برگشت به سمت خروجی) ادامه مییابد. در انتها، سیال از طریق مجرای خروجی کلگی جلو به بیرون از مبدل هدایت میشود. به سیالی که این مسیر را طی میکند، سیال سمت لوله میگویند. این سیال، به غیر از نواحی کلگی جلو و عقب، هیچ تماس مستقیمی با بدنه محفظه نخواهد داشت.
سیال سمت پوسته
«سیال سمت پوسته» (Shell Side Fluid)، سیالی است که از طریق مجرای ورودی روی پوسته به محفظه تحت فشار وارد میشود. این سیال با عبور از بافل و مسیر طراحی شده، با سطح لولهها تماس مییابد. در انتها، پس از تبادل حرارت با سیال درون لولهها، از طریق مجرای دیگر روی پوسته خارج میشود.
صفحه تقسیم کننده مسیر
«تقسیم کننده مسیر» (Pass Divider) یا «صفحه تقسیم کننده» (Partition Plate)، قطعهای است که در مبدلهای حرارتی دارای دو مسیر لوله به کار گرفته میشود. در صورت ساخت کانال یا کلگی به روشهای ریخته گری یا دایکاست، تقسیم کننده مسیر در طراحی قالب و قطعه در نظر گرفته میشود. در صورت ساخت کانال یا کلگی توسط نورد یا برشکاری لوله، تعبیه تقسیم کننده مسیر در محل مورد نظر، به کمک جوشکاری انجام میگیرد.
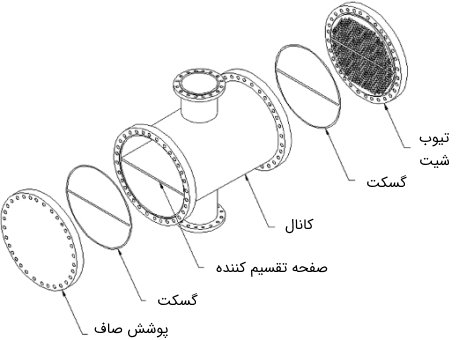
انتخاب پیکربندی صفحات تقسیمکننده در مبدلهای حرارتی چند مسیره، کاملا اختیاری است. با این وجود، پیکربندی مناسب تقسیم کنندهها باید دارای ویژگیهای زیر باشد:
- وجود تعداد برابری از لولهها در هر مسیر
- به حداقل رساندن کاهش تعداد لولهها در سطح مقطع هر مسیر
- به حداقل رساندن اختلاف فشار در راستای هر یک از تقسیم کنندهها
- فراهم کردن سطح اتصال کافی برای درزبند
- به حداقل رساندن پیچیدگیها و هزینه ساخت
بافل مبدل حرارتی پوسته و لوله
سِپَرک یا «بافل» (Baffle)، قطعهای درون محفظه مبدل حرارتی پوسته و لوله است که به منظور نگهداری لوله و هدایت جریان مورد استفاده قرار میگیرد. کاربردهای بافل عبارت هستند از:
- نگهداری لولهها در محل مناسب طی مراحل ساخت و اجرا به منظور جلوگیری از ارتعاش لولهها بر اثر جریانهای متلاطم
- هدایت رفت و برگشتی سیال سمت پوسته در راستای ناحیه دربرگیرنده لوله برای افزایش سرعت و ضریب انتقال حرارت
- حفظ فاصله بین لولهها
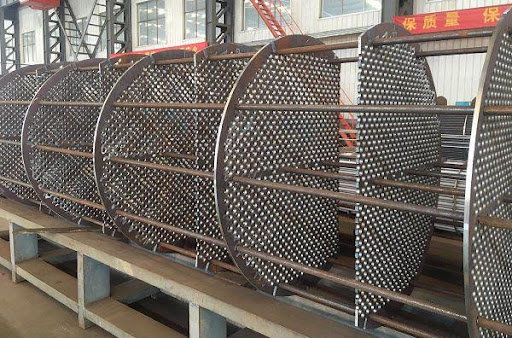
بافل کات
برش بافل یا «بافل کات» (Baffle Cut)، بخشی است که در آن، جهت جریان سیال، موازی با محور لولهها میشود. طول بهینه برای این بخش، حدود ۲۵ درصد از قطر پوسته است. طراحی برش بافل با طول کمتر یا بیشتر، سیال سمت لوله را با مشکلاتی نظیر اغتشاش جریان، تشکیل ناحیه مرده پشت بافل و افت فشار بیش از حد مواجه میکند.

گام بافل
فاصله بین بافلها با عنوان گام بافل شناخته میشود. گام و برش بافل بر روی سرعت جریان، نرخ انتقال حرارت و افت فشار تاثیر میگذارند. تعیین این دو پارامتر در حین طراحی مبدل و به منظور دستیابی به حداکثر سرعت و نرخ انتقال حرارت ممکن با توجه به افت فشار مجاز صورت میگیرد. در صورت طراحی مناسب گام، مساحت نواحی جریان آزاد در فاصله بین لبه بافل تا پوسته و دسته لولهها تقریبا برابر میشوند.
انواع بافل
یکی از معیارهای تقسیمبندی بافلها در مبدل های حرارتی پوسته و لوله، جهت برش آنها است. در مبدلهای حرارتی افقی، جهت گیری برش بافل اهمیت دارد. در صورت محسوس بودن حرارت و عدم تغییر فاز سیال سمت پوسته، برش بافل باید به صورت افقی باشد. در این پیکربندی مسیر، حرکت سیال در جهت بالا و پایین، از لایهبندی سیال (تجمع سیال گرمتر در بالا و سیال سردتر در پایین) جلوگیری میکند. برای میعان سیال سمت پوسته، بافل کات به صورت عمودی و برای سیال در حال جوش سمت پوسته، برش بافل از نوع افقی یا عمودی است.
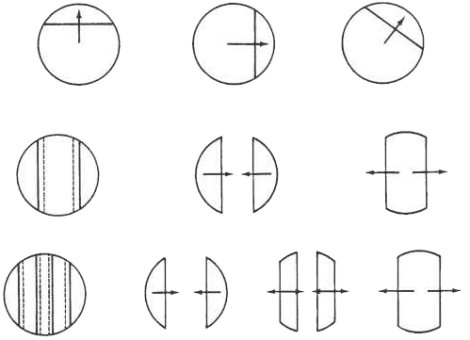
در بسیاری از سیالات گازی پرسرعت، پیکربندی بافل با یک قطعه میتواند باعث افزایش قابل توجه افت فشار شود. یکی از روشهای رفع این مشکل، استفاده از بافلهای چند بخشی است (ردیف میانی و پایینی در تصویر بالا). در تجهیزات بسیار بزرگ، امکان استفاده از پیکربندی سه تکهای و حتی میلهای بافل وجود دارد. نکته مهم در به کارگیری انواع بافل، رعایت موقعیت مناسب لولهها و گام آنها است. از دیگر انواع بافل برای شرایط خاص میتوان به بافلهای مارپیچی، EM (فلز انبساطی) و عرضی است.
میله های نگهدارنده
میلههای نگهدارنده، قطعاتی هستند که به منظور نگهداری اجزای بافل در کنار یکدیگر و حفظ گام بافل مورد استفاده قرار میگیرند. یک طرف میلههای نگهدارنده به صفحه لوله و طرف دیگر آنها به آخرین بافل فیکس میشود. به منظور حفظ گام، بافلها بر روی قطعاتی با عنوان اسپیسر قرار میگیرند. حداقل تعداد میله نگهدارنده و اسپیسر، به قطر پوسته و ابعاد میلهها بستگی دارد.
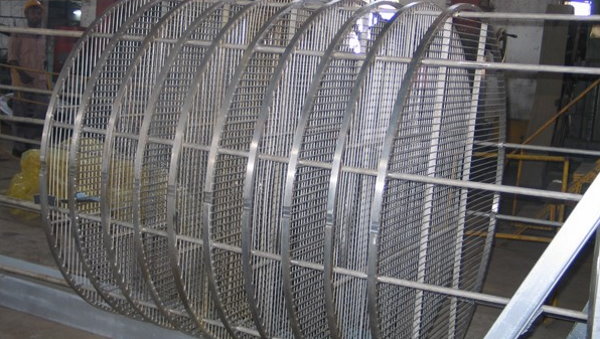
انواع مبدل های حرارتی پوسته و لوله چه هستند؟
از متداولترین انواع مبدل های حرارتی پوسته و لوله بر اساس ساختار اجزا میتوان به مبدلهای حرارتی با لولههای U شکل، مبدلهای حرارتی با تیوب شیت ثابت و مبدلهای حرارتی با کلگی شناور اشاره کرد. البته معیارهای دیگری برای دستهبندی انواع مبدلهای حرارتی پوسته و لوله نیز وجود دارند که در این بخش به معرفی برخی از آنها میپردازیم.
انواع مبدل حرارتی پوسته و لوله بر اساس استاندارد TEMA
مبدل های حرارتی پوسته و لوله، بر اساس استاندارد TEMA، به سه گروه مبدلهای کلاس B، مبدلهای کلاس C و مبدلهای کلاس R تقسیم میشوند. هر یک از این کلاسها، روش ساخت، ساختار پوسته و نوع کاربری مبدل را مشخص میکنند.
- کلاس B: مبدل های حرارتی پوسته و لوله مورد استفاده در فرآیندهای شیمیایی
- کلاس C: مبدل های حرارتی پوسته و لوله با کاربری عمومی در صنایع مختلف
- کلاس R: مبدل های حرارتی پوسته و لوله مورد استفاده در صنایع پتروشیمی و فرآیندهای بزرگ مقیاس
علاوه بر کلاسهای بالا، انواع جزئیتر مبدلهای حرارتی در استاندارد TEMA با حروف مشخص میشوند. در بخش استانداردهای مبدل های حرارتی پوسته و لوله، بیشتر راجع به دستهبندی TEMA توضیح میدهیم.
انواع مبدل حرارتی پوسته و لوله بر اساس مکانیزم جریان سیال
یکی از معیارهای دستهبندی مبدل های حرارتی پوسته و لوله، تقسیمبندی آنها بر اساس مکانیزم عملکرد آنها، نظیر نحوه جریان یافتن سیال است. با توجه به این معیار، مبدلهای حرارتی پوسته و لوله به انواع مبدل حرارتی جریان موازی یا همسو، مبدل حرارتی جریان مخالف یا ناهمسو و مبدل حرارتی جریان متقاطع تقسیم میشوند. در برخی از موارد، با توجه به طراحی، اجرا و کاربری تجهیزات، امکان استفاده ترکیبی از این جریانها وجود دارد.

مبدل حرارتی پوسته و لوله جریان همسو
در مبدلهای حرارتی دارای «جریان موازی» (Parallel Flow) یا «جریان همسو» (Cocurrent Flow)، سیال سمت پوسته و سیال سمت لوله از یک طرف وارد مبدل میشوند و به سمت طرف مقابل حرکت میکنند. میزان تغییرات دما برای هر سیال یکسان است.
مبدل حرارتی پوسته و لوله جریان ناهمسو
در مبدلهای حرارتی دارای «جریان مخالف» (Counter Flow) یا «جریان ناهمسو» (Countercurrent Flow)، سیال سمت پوسته و سیال سمت لوله از دو سمت مخالف یکدیگر وارد سیستم شده و از سمت مقابل خارج میشوند. این سیستم، متداولترین و کارآمدترین مکانیزم جریان در مبدلهای حرارتی به شمار میرود.
مبدل حرارتی پوسته و لوله جریان متقاطع
در مبدلهای حرارتی دارای «جریان متقاطع» (Cross Flow)، زاویه راستای حرکت سیال سمت پوسته نسبت به راستای حرکت سیال سمت لوله برابر ۹۰ درجه است. در این سیستم، یکی از سیالات در حین عبور از مسیر مشخص شده، تغییر فاز (مایع به گاز) میدهد و سپس، توسط سیال باقی مانده در حالت مایع جذب میشود.
مبدل حرارتی پوسته و لوله با تیوب شیت ثابت
مبدل حرارتی پوسته و لوله ثابت، از لولههای مستقیم تشکیل میشود که هر دو انتهای آنها به صفحات لوله محکم شدهاند. در این نوع مبدل حرارتی، اتصال صفحه لوله یا تیوب شیت به پوسته توسط جوشکاری انجام میگیرد. مبدل های حرارتی پوسته و لوله مستقیم از طراحی و ساخت ساده بهره میبرند. به علاوه، هزینه این نوع مبدلهای حرارتی کمتر از انواع دیگر است.
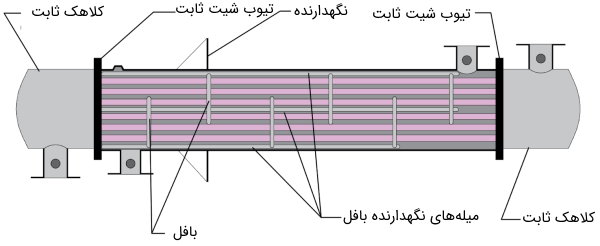
در صورت وجود اختلاف دمایی بالا بین سیالات، ساختار مبدل حرارتی پوسته و لوله با تیوب شیت ثابت تحت تاثیر قرار میگیرد. البته با اضافه کردن درز انبساطی، این مشکل برطرف میشود. از مهمترین مزایای مبدلهای حرارتی پوسته و لوله ثابت میتوان به تمیزکاری و نگهداری ساده این تجهیزات اشاره کرد.
مزایا و معایب مبدل های حرارتی پوسته و لوله با تیوب شیت ثابت
از مزیتهای مبدل های حرارتی پوسته و لوله با تیوب شیت ثابت میتوان به موارد زیر اشاره کرد:
- سادگی و به صرفه بودن روش ساخت
- به حداقل رسیدن درزهای نیازمند آببندی
- به حداقل رسیدن احتمال نشت به دلیل جوشکاری پوسته به تیوب شیت از هر دو سمت
- عدم اختلاط سیال سمت پوسته و سمت لوله
- عدم محدودیت در تعداد مسیرهای عبور سیال سمت لوله
- سادگی جایگزینی لولهها به دلیل ساختار مستقیم آنها
- امکان تمیزکاری مکانیکی و شیمیایی
- کم بودن میزان انحراف سیال سمت پوسته در ناحیه بین باندل و پوسته
محدودیتهای مبدل های حرارتی پوسته و لوله با تیوب شیت ثابت شکل عبارت هستند از:
- عدم امکان در آرودن باندل برای بازرسی و تمیزکاری
- عدم امکان تمیزکاری دستی یا مکانیکی سطح خارجی لولهها
- الزام استفاده از پوسته و تیوب شیت قابل جوش
مبدل حرارتی پوسته و لوله U شکل
مبدل حرارتی U شکل، از لولههایی با پیکربندی U شکل تشکیل میشود. ولوهای ورودی و خروجی لولهها، در یک طرف مبدل قرار دارند. ورود سیال از بالای نیمه بالایی و خروج آن از نیمه پایین صورت میگیرد. در بخش U شکل، امکان انبساط لوله وجود دارد. این ویژگی، امکان استفاده از مبدل حرارتی U شکل در شرایطی با اختلاف دمای بالا را فراهم میکند.
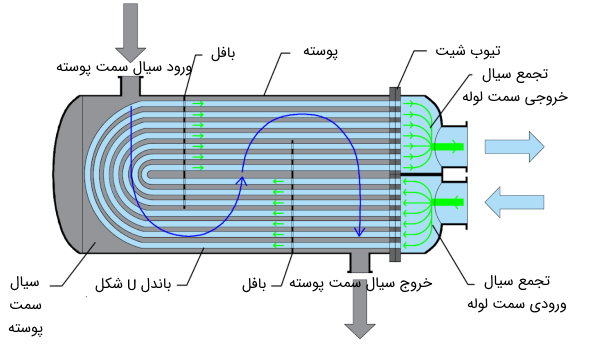
پیکربندی ولوهای ورودی و خروجی مبدل های حرارتی پوسته و لوله U شکل، با توجه به طراحی مبدل تعیین میشود. به عنوان مثال، در تصویر بالا، ورود سیال سمت پوسته، از ولو تعبیه شده در بالا-چپ پوسته و خروج آن از ولو تعبیه شده در پایین-راست پوسته صورت میگیرد.
مزایا و معایب مبدل های حرارتی پوسته و لوله U شکل
از مزیتهای مبدل های حرارتی پوسته و لوله U شکل میتوان به موارد زیر اشاره کرد:
- هزینه اولیه پایین
- حذف درز بندی داخلی و جایگزینی راحت درزبندهای خارجی
- نیاز به یک تیوب شیت
- امکان در آوردن باندل برای تمیزکاری و بازرسی
- به حداقل رسیدن انحراف سیال سمت پوسته به دلیل فاصله کم بین پوسته و لولههای خارجی
- تمیزکاری راحت کانال، سریهای سمت لوله
محدودیتهای مبدل های حرارتی پوسته و لوله U شکل عبارت هستند از:
- استفاده از مواد شیمیایی برای تمیزکاری سطوح داخلی لولهها
- دشوار بودن جایگزینی هر لوله
- کم بودن تعداد لولههای قابل فیکس بر روی تیوب شیت به دلیل خمهای U شکل
- عدم امکان افزایش یا کاهش مسیرهای سیال سمت لوله
- احتمال شروع فرسایش سطوح داخلی خمها به دلیل سرعت سیال در حین چرخش
مبدل حرارتی پوسته و لوله با یک سر شناور
مبدل های حرارتی پوسته و لوله با یک سر شناور، مشابه مبدلهای حرارتی پوسته و لوله U شکل هستند. با این تفاوت که در این مبدلها، پیکربندی لولهها، U شکل نبوده و مستقیم است. در این مبدلها، فقط یک سر لولهها به تیوب شیت ثابت متصل میشود. آزاد بودن سر دیگر لولهها، امکان انبساط و شناور شدن آنها را فراهم میکند.
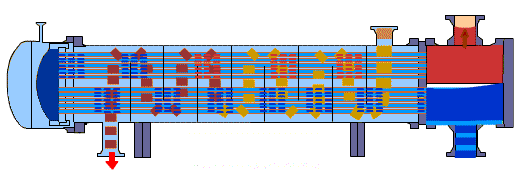
مبدل های حرارتی پوسته و لوله شناور، قادر به عملکرد در اختلاف دمای بالا هستند. به دلیل ساده بودن نحوه باز و بسته کردن اجزا، تمیزکاری و بازرسی این نوع مبدل حرارتی ساده است. از انواع مبدلهای حرارتی با سر شناور میتوان به موارد زیر اشاره کرد:
- مبدل حرارتی پوسته و لوله نوع T
- مبدل حرارتی پوسته و لوله نوع S
- مبدل حرارتی پوسته و لوله نوع P
- مبدل حرارتی پوسته و لوله نوع W
مبدل حرارتی پوسته و لوله نوع T
در مبدل های حرارتی پوسته و لوله نوع T، امکان بیرون کشیدن تیوب باندل از پوسته وجود دارد. در این مبدل، اختلاف بین قطر بافل باندل با قطر داخلی پوسته اصلی بسیار زیاد است. تصویر زیر، پیکربندی این نوع مبدل حرارتی پوسته و لوله را به خوبی نمایش میدهد.
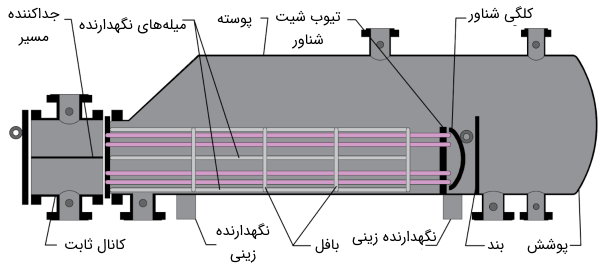
مبدل حرارتی پوسته و لوله نوع S
پیکربندی مبدل های حرارتی پوسته و لوله نوع S به گونهای است که برای خروج باندل از پوسته، باید اجزای باندل را به طور کامل باز کرد. در این نوع مبدل، فاصله بین قطر بافل و پوسته، معمولی است.
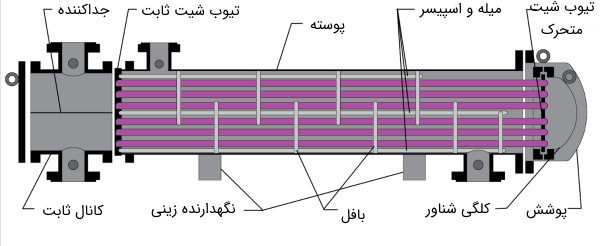
مبدل حرارتی پوسته و لوله نوع P
در مبدل های حرارتی پوسته و لوله نوع P، اجزای سمت پوسته توسط رینگهای آببندی، درزبندی میشوند و درون محفظه آببندی قرار میگیرند. این پیکربندی، امکان جابجایی رفت و برگشتی تیوب شیت را فراهم میکند.
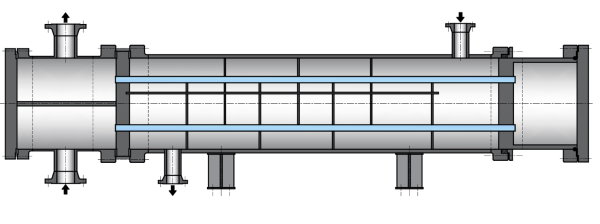
مبدل حرارتی پوسته و لوله نوع W
مبدل های حرارتی پوسته و لوله نوع W، دو سیال توسط اورینگ، آببندی شده و توسط رینگ فانوسی، از یکدیگر جدا شدهاند.
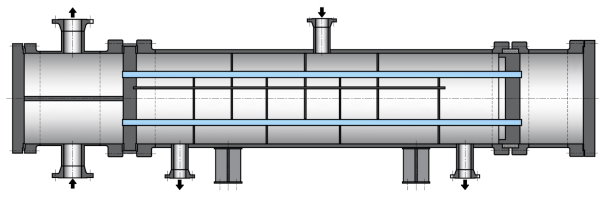
مزایا و معایب مبدل های حرارتی پوسته و لوله با یک سر شناور
از مزیتهای مبدل های حرارتی پوسته و لوله با یک سر شناور میتوان به موارد زیر اشاره کرد:
- امکان در آوردن باندل برای بازرسی
- سهولت تمیزکاری مکانیکی سطح خارجی لولهها
- امکان عوض کردن هر لوله به دلیل مستقیم بودن ساختار
- تمیزکاری سطح داخلی لولهها، بدون نیاز به در آوردن باندل
- عدم محدودیت در تعداد مسیرهای سیال سمت لوله
محدودیتهای مبدل های حرارتی پوسته و لوله با یک سر شناور عبارت هستند از:
- هزینه زیاد
- تعداد زیاد درزبند
استاندارد مبدل های حرارتی پوسته و لوله چیست؟
به طور کلی، استانداردهای بهداشتی ۳A، موسسه نفت آمریکا (API)، انجمن سازندگان مبدلهای لولهای (TEMA)، انجمن مهندسان مکانیک آمریکا (ASME) و دایرکتیو تجهیزات فشار از جمله دستورالعملهای بینالمللی پرکاربرد در رابطه با مبدل های حرارتی پوسته و لوله به شمار میروند. البته استاندارد مورد استفاده برای طراحی، ساخت و اجرای مبدلهای حرارتی پوسته و لوله به صنایع هدف بستگی دارد. به عنوان مثال، در صنایع غذایی و داروسازی، بهداشت و ایمنی محصولات برای مصرفکنندگان، از اهمیت بسیار بالایی برخوردار است. از اینرو، عملکرد این صنایع و تجهیزات مورد استفاده در آنها، به طور جدی تحت نظارت سازمان غذا و دارو (FDA) قرار میگیرند.
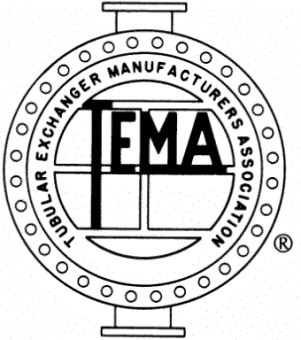
استاندارد TEMA
استانداردهای «انجمن سازندگان مبدلهای لولهای» (Tubular Exchangers Manufacturers Association) یا TEMA، متداولترین و پرکاربردترین منابع مورد استفاده برای طراحی، ساخت و اجرای مبدل های حرارتی پوسته و لوله محسوب میشوند. این استانداردها، اطلاعات مخصوص تمام پیکربندیهای مبدلهای حرارتی پوسته و لوله، به علاوه سه دستهبندی برای انواع صنعتی این مبدلها را ارائه میکنند.
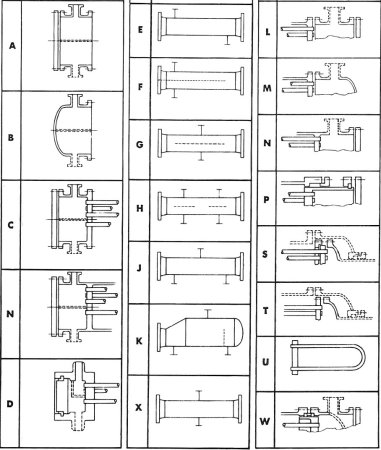
استاندارد TEMA از ساختار کلگی عقب، کلگی جلو و پوسته برای تقسیمبندی و شناسایی مبدل های حرارتی پوسته و لوله استفاده میکند (تصویر بالا). به منظور تشخیص راحت طراحیها و پیکربندیهای متفاوت، نوع مبدل حرارتی با سه حرف (مانند BEM یا AEM) بیان میشود. معنی هر حرف عبارت است از:
- حرف اول کد مبدل حرارتی پوسته و لوله: توصیف نوع کلگی ثابت و نحوه اتصال تیوب شیت به پوسته و کانال (پیچی یا جوشی)
- حرف دوم کد مبدل حرارتی پوسته و لوله: توصیف نوع پوسته، محل قرارگیری مجراها، حضور بافلهای طولی و صفحات توزیع جریان
- حرف سوم کد مبدل حرارتی پوسته و لوله: توصیف نوع کلگی عقب، نحوه اتصال پوسته با تیوب شیت دوم و سیستم بستن کانال (پیچی یا جوشی)
بر اساس استاندارد TEMA، مبدل حرارتی پوسته و لوله BEM، از یک کلگی دارای کلاهک (درپوش)، پوسته یکطرفه و تیوب شیت ثابت تشکیل میشود.
استانداردهای بهداشتی ۳A
استانداردهای بهداشتی ۳A یا ۳ASSI، دستورالعملهای مورد استفاده در صنایع غذایی، لبنیات و داروسازی هستند. این دستورالعملها بر روی تمیزکاری ساده تجهیزات و امکان شستشوی برجا (CIP) آنها تمرکز میکنند. مجموعه استانداردهای ۳ASSI، حدود ۷۰ استاندارد از جمله استاندارد مبدل های حرارتی را پوشش میدهند.
استاندارد API۶۶۰
استاندارد شماره ۶۶۰ انجمن نفت آمریکا یا API۶۶۰، دستورالعمل طراحی، انتخاب مواد، ساخت، بازرسی، آزمایش و ترابری مبدلهای حرارتی پوسته و لوله در صنایع نفت و پتروشیمی ارائه میکند. این استانداردها برای مبدلهای حرارتی، کوندانسورها، کولرها و ریبویلرها قابل استفاده هستند. استاندارد ISO ۱۶۸۱۲، معادل بین المللی استاندارد API۶۶۰ است.
استاندارد ASME Section VIII
استاندارد ASME Section VIII از مجموعه استانداردهای «انجمن مهندسان مکانیک آمریکا» (American Society of Mechanical Engineers)، به اجزای تحت فشار مبدل های حرارتی پوسته و لوله (لولههای داخل پوسته) اشاره دارد. این استاندارد، به طور گسترده برای طراحی، ساخت و اجرای مبدلهای مذکور مورد استفاده قرار میگیرد. البته استانداردهای استاندارد ASME Section II و استاندارد ASME Section V نیز در فرآیند انتخاب مواد و آزمایش مبدلها کاربرد دارند. استاندارد EN ۱۳۴۴۵، معادل استاندارد ASME Section VIII در سیستم اروپایی است.
دایرکتیو تجهیزات فشار
«دایرکتیو تجهیزات فشار» (Pressure Equipment Directive) یا PED، یکی از استانداردهای بینالمللی مبدل های حرارتی پوسته و لوله به شمار میرود. این استاندارد قوانین مرتبط با انتخاب مواد، استانداردهای سازگار، الزامات اساسی، نظارت بازار و ارزیابی انطباق را ارائه میکند. هدف اصلی از رعایت قوانین معرفی شده در PED، تامین ایمنی محصولات و کارکنان درگیری با مبدلهای حرارتی است.
مزایای مبدل های حرارتی پوسته و لوله چه هستند؟
مبدل های حرارتی پوسته و لوله از هزینه نسبتا پایین، ظرفیت مناسب، بازه گسترده فشار و دمای عملیاتی، مقاومت در برابر خوردگی و انعطاف پذیری در طراحی بهره میبرند. همین ویژگیها، باعث محبوبیت و رواج این نوع مبدل حرارتی در صنایع مختلف شده است.
هزینه
هزینه مبدل های حرارتی پوسته و لوله، بسیار کمتر از مبدلهای حرارتی صفحهای است. این ویژگی به همراه بازدهی خوب، مبدلهای حرارتی پوسته و لوله را به متداولترین و محبوبترین گزینه در صنایع مختلف تبدیل کردهاند.
ظرفیت
مبدلهای حرارتی باید قادر به فعالیت در دماهای عملیاتی مختلف (بر اساس کاربری مورد نیاز) باشند. قابلیت این مبدلها در تحمل دماهای بالا، امکان کنترل تولید و پیشروی عملیات را فراهم میکند. مبدل های پوسته و لوله، ظرفیت عملیاتی بالایی دارند و میتوانند در هر شرایط دمایی به کار گرفته شوند.
فشار و دمای عملیاتی
فشار بالا، ایمنی سیستم و نرخ تولید را تحت تاثیر قرار میدهد. مبدل های حرارتی پوسته و لوله به منظور تحمل فشارهای بسیار بالا و دستیابی به حداقل افت فشار ممکن طراحی و ساخته میشوند. ویژگی مذکور به همراه مقاومت بالا در برابر دماهای زیاد، کاربری این مبدلها در صنایع مختلف را افزایش میدهد.
مقاومت در برابر خوردگی
استفاده از آندهای گالوانی یا فداشونده در ساخت مبدل های حرارتی پوسته و لوله، باعث ایجاد یک لایه مقاوم بر روی سطح میشود. مقاومت در برابر خوردگی و فرسودگی، دوام و طول عمر اجزای مختلف این مبدلهای حرارتی را بهبود میبخشد.
انعطاف پذیری طراحی
از نقطه نظر طراحی، مبدل های حرارتی پوسته و لوله، بیشترین انعطافپذیری را نسبت به دیگر انواع مبدلهای حرارتی دارند. طراحی مبدلهای حرارتی پوسته و لوله را میتوان بر اساس کاربری در فرآیند مورد نظر تغییر داد. تغییر در قطر، تعداد، گام و پیکربندی لولهها، از متداولترین روشهای تغییر کاربری این مبدلها است.
انبساط حرارتی
با طراحی مبدل های حرارتی پوسته و لوله به صورت چند تیوبه، مانعی برای انبساط حرارتی بین لوله و پوسته وجود نخواهد داشت. این پیکربندی، امکان استفاده از سیالات قابل اشتعال و سمی را فراهم میکند.
ناحیه تحت پوشش
مبدل های حرارتی پوسته و لوله، با وجود طول کمتر به دلیل حضور چندین لوله، سطح بزرگتری را برای انتقال حرارت پوشش میدهند.
معایب مبدل حرارتی پوسته و لوله
محدودیتهای مبدلهای حرارتی پوسته و لوله عبارت هستند از:
- نگهداری: تمیز کردن لولههای مبدل های حرارتی پوسته و لوله دشوار است. به علاوه، وجود رسوب بر روی ضریب انتقال حرارت تاثیر زیادی میگذارد. از اینرو، پوسته و لوله باید در دورههای مشخص تمیز شوند. در صورت مثلثی بودن گام مبدل، پیچیدگی فرآیند نگهداری و تمیزکاری افزایش مییابد.
- بهرهوری: بازدهی مبدلهای حرارتی پوسته و لوله نسبت به مبدلهای حرارتی صفحهای کمتر است.
- توسعه ظرفیت: امکان افزایش ظرفیت مبدلهای حرارتی پوسته و لوله وجود ندارد.
- ابعاد: عدم وجود خمهای سنجاقی در مبدلهای حرارتی پوسته و لوله، باعث افزایش ابعاد آنها نسبت انواع صفحه میشود. در ظرفیتهای پایینتر، این مبدلها، فضای بیشتری را اشغال میکنند.
سوالات متداول مبدل های حرارتی پوسته و لوله
در این بخش، به برخی از متداولترین پرسشهای مرتبط با مبدل های حرارتی پوسته و لوله پاسخ میدهیم.
مبدل حرارتی پوسته و لوله از چه موادی ساخته میشوند؟
مبدل های حرارتی پوسته و لوله، از مواد رسانای گرمایی با قابلیت انتقال راحت حرارت ساخته میشوند. علاوه بر این، مواد مورد استفاده باید در برابر اثرات فرسایش و خوردگی مقاوم باشند. به طور کلی، نوع ماده، به نوع سیال بستگی دارد. فولاد ضد زنگ و مس، از رایجترین مواد مورد استفاده برای پوسته لولههای مبدل حرارتی به شمار میروند. البته، برنج نیز یکی از گزینههای ساخت پوسته است.

سیالات مورد استفاده در مبدل حرارتی پوسته و لوله چه هستند؟
از سیالات رایج در مبدل های حرارتی پوسته و لوله میتوان به بخار، روغن هیدرولیک، آب دیونیزه، روغن ماشین، آب نمک و روغن موتور اشاره کرد.
ابعاد مبدل حرارتی پوسته و لوله چقدر است؟
هیچ محدودیتی در ابعاد مبدل های حرارتی پوسته و لوله وجود ندارد. طول کلی این تجهیزات، معمولا تا ۲۲۰ سانتیمتر و مساحت سطح اشغالی آنها تا ۸٫۶ متر مربع است. قطر پوسته نیز میتواند به حدود ۶۱ سانتیمتر برسد.
اتصالات سمت پوسته مبدل حرارتی پوسته و لوله از چه نوعی است؟
اتصالات سمت پوسته مبدل های حرارتی پوسته و لوله، معمولا از نوع پیچی یا فلنجدار است.
دما و فشار عملیاتی مبدل حرارتی پوسته و لوله چقدر است؟
فشار عملیاتی مبدل های حرارتی پوسته و لوله به ماده سازنده پوسته (مخزن تحت فشار) بستگی دارد. بر این اساس، فشار پوسته بین ۶٫۹ بار تا ۶۹ بار تغییر میکند. دمای عملیاتی مبدلهای حرارتی پوسته و لوله نیز معمولا بین ۲۵۰ تا ۸۰۰ درجه سانتیگراد طراحی میشود.
سیال خنک کننده در مبدل حرارتی پوسته و لوله چیست؟
از رایجترین سیالات خنک کننده در مبدلهای حرارتی پوسته و لوله میتوان به آب، پروپیلن گلیکول و اتیلن گلیکول اشاره کرد. آب، به عنوان متداولترین سیال خنککننده شناخته میشود. این سیال، موثرترین گزینه برای اغلب کاربریها است. آب، عملکرد بسیار مناسب در انتقال حرارت بهره میبرد و هزینه بسیار پایینی دارد. ترکیب آب با پروپیلن گلیکول یا اتیلن گلیکول نیز به منظور سیال خنک کننده در شرایط دمایی شدید مورد استفاده قرار میگیرد. در البته مواد سمی موجود در پروپیلن گلیکول کمتر از اتیلن گلیکول است.
قیمت مبدل حرارتی پوسته و لوله چقدر است؟
قیمت مبدل های حرارتی پوسته و لوله، با توجه به مساحت سطح، ابعاد لولهها، حداقل/حداکثر فشار/دمای عملیاتی، ظرفیت سرمایش/گرمایش، تعداد مسیرهای سیال، نصب، نگهداری و غیره، معمولا بین ۶۰۰ تا ۸۰۰۰ دلار است. به خاطر متغیر بودن نرخ ریال در مقابل دلار میتوانید قیمت روز دلار را به معادل ریالی آن تبدیل کنید.
کاربرد اصلی مبدل حرارتی پوسته و لوله چیست؟
با وجود کاربریهای متعدد، مبدل های حرارتی پوسته و لوله، اغلب در تاسیسات گرمایشی و سرمایشی نظیر سیستم خنکسازی موتور و سردخانهها مورد استفاده قرار میگیرند.
بهترین مبدل حرارتی پوسته و لوله چگونه انتخاب میشود؟
بهترین مبدل های حرارتی پوسته و لوله برای کاربری مورد نظر با توجه به سطح تعمیر و نگهداری (دورههای تمیزکاری)، سهولت تعمیر نگهداری (سازگاری با استاندارد)، فشار و دمای عملیاتی، ماهیت سیال (رسوبکننده، تمیز، خورنده، ویسکوز) و فاز سیالات (گاز-گاز، مایع-بخار، مایع-مایع و غیره) انتخاب میشود.
آزمایش مبدل حرارتی پوسته و لوله چیست؟
از آزمایشهای رایج برای کنترل کیفیت مبدل های حرارتی پوسته و لوله برای طراحی، ساخت و بازرسی میتوان به رادیوگرافی، مایع نافذ، هیدرولیک و نشت هوا اشاره کرد.